posted by
rerofumi
2012/7/25 水曜日 21:00:59
背中がかゆくなった。
しかし、そんなときいつも使っていたアルミ定規がどっかにいってしまった。どこいってしまったんだろう。
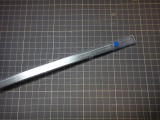
そんなとき ICレールで掻くのが通という声もある。まあ確かに使うことはあるが、これ結構とがっていて痛いのだよな。
ここは素直に「まごの手」を入手するか。まごの手ってどこ行けば買えるのだ?Amazonでは確かに買えるけれども、まごの手風情を Amazon でいうのも大仰な気がする。
……こういう身近な日用品は家庭内で3Dプリントできるべきなんじゃないかな。
というわけで「まごのて」を作ってみるよ。
といっても廉価な3Dプリンターでは長いものが作れない。Makerbot Replicator ではテーブルが大きくなったといっても 15cm 強くらいのがせいぜい。
一般的な孫の手って長さどれくらい?と調べてみると 40cm くらいはあった方が良いらしい。なので、3Dプリンターでの出力品をつないで伸ばす事を考える。
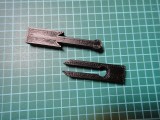
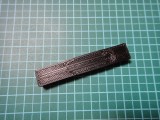
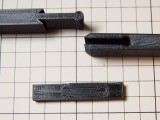
つないで伸ばすための「継ぎ」をいくつか考えたり作ってみたりしたのだけれども、最終的にこういう形になった。
あそび無くはまるものを作るのは難しく、使う3Dプリンターの癖を加味しないといけないので、今回はあくまでうちの Makerbot Replicator で出力したときに填まるものという設計。
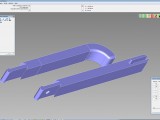
継ぎができたらそれをCAD上で伸ばすようにして設計。
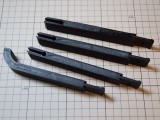
3Dプリンターで出力して

完成。
ABS なんでしなるし、たわんでも壊れない適度な厚さで良い感じに作れた。
これでまごのてを買わなくても済んだぞ。
形状データは Thingivers に置いてあるのでよろしく。
MAGONOTE (Backscratcher) http://www.thingiverse.com/thing:27371
posted by
rerofumi
2012/7/21 土曜日 16:05:16
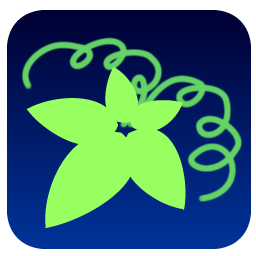
Gynostemma で KiCAD のゾーン(ベタ塗りつぶし)が適用されないという報告をいただいた。
KiCAD から適当なサンプルを出力してガーバーを確認してみると、拡張コードの G36/G37 にあたる「ポリゴン領域指定」を使用していることがわかった。
確かにこの命令には未対応である。
回避策はあるものの機能として未対応なのはイマイチなので、今回はポリゴンフィルに対応させてみることにした。
Gynostemma でポリゴン領域を読み込んだら、ハッチ(ラインを並べて塗りつぶす)に変換して扱うという若干暫定的な対応。
Download: gynostemma-20120721.zip (1.34MB) マルチスレッド、ポリゴン対応版
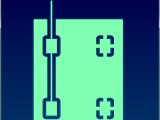
ハッチは線を密に並べて埋め尽くすというものなので、形状が爆発的に増えてそれだけ処理時間が増大するので今ひとつ良い対応でもなかったりする。
ポリゴンフィルの情報など。
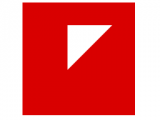
KiCAD のゾーンでは穴あきのポリゴンも出力できる。
どういう仕組みかと見てみたら、
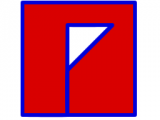
このような出力になっていた。
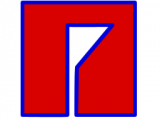
わかりやすく手直しするとこういう感じ。
確かに一筆書きの多角形ポリゴンではあるけれども、凹みがある複雑な形状に分類される類いのものであった。
Gynostemma は内部でパターンを三角形ポリゴン化して扱っているので、ポリゴンフィルもハッチではなくポリゴンとして扱った方が処理は軽くなるはずである。
しかし、上記のような複雑なポリゴンを三角形分割する低コストなアルゴリズムが思いつかなかったので今回はハッチ変換とした次第。
このへん思うところあるので、もうちょっといじって見る予定。
posted by
rerofumi
2012/7/15 日曜日 18:00:12
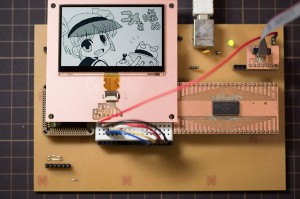
秋月電子通商の新製品一覧を見ていたら「シャープ モノクロHR-TFTメモリ液晶モジュール 2.7インチ WQVGA [LS027B4DH01]」なるものが出ていた。
うおお、これは面白そうだ。何か作品を作るのでは無くて単に使ってみたい!
と思ったので買って表示させてみましたというのが今回の工作記事。
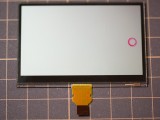
大きさ的には 6cm×4cm ほどのモノクログラフィック液晶モジュール。
赤い丸は保護シートの模様。
低消費電力が売りになっているのは、バックライトがない反射型液晶だというのと画素メモリがあってリフレッシュなしでも画像を保持できるため駆動間隔を妙に長く取れてその分電力を食わないということらしい。同じ絵を出し続けるならリフレッシュなしで2時間くらいはほっておけるらしい。
まあ普通のLCDモジュールでもドライバー内にバッファがあって勝手にリフレッシュしてくれているから、マイコン工作として制御する分の手間は大して変わらない感じ。メリット的には 400x240pixel という高精細なモノクロLCDが手に入るというあたりではないかと。
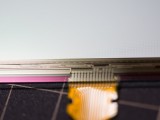
裏面から見た写真。
これガラス基板の上にドライバーが構築されているのか。
昔シャープが「ガラスの上にZ80を構築できました!」とアピールしていたが、その技術がこんな風に使われていたのね。この液晶モジュールのシリアル通信駆動速度は max 2MHz なんだそうだけれども、その速度もガラス基板回路と考えると順当かも。
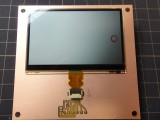
取り敢えずのテストで絵を出すにも、まずは breakout ボードを作らないといけない。
秋月で買うと面実装のフレキコネクタが 1個だけ付いてくる。これが 10p 0.5mm ピッチなのでなんとかそれっぽい変換基板を使って利用する形になるだろう。
こんな時に頼もしいのが自作基板である :-)
というわけで私はCNCフライスを使っての自作基板でコネクタを取り付けられる様な brekeout 基板を作ってみた。
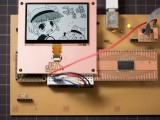
今回はなんでもいいから表示だけしてみようという実験なので、自作の PSoC3 テストボードを利用する。
ブレッドボード部分に挿して簡易テスト配線。
LCDモジュールの電源は 5V 単一、信号線は 5V でもいいけどできるだけ 3V 前後にしてくれと不思議な指示がある。今回は 3.3V のシグナルを利用。
コントロールに必要なのは
シリアルクロック・シリアルデータ・チップセレクト(シリアル送信中にHになる)、LCD表示コントロール
の 4本のみ。
シリアルクロックとシリアルデータは SPI の tx オンリーと見て良い。
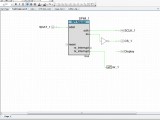
PSoC Creater でのブロック設計はこんな感じで SPI 1個。
チップセレクトは SPI ブロックの SS 出力タイミングで良かったのだけれども、モジュールと H/L が逆なので NOT を追加している。PSoC 便利だねえ。
転送終了の割り込みを受け取れるかと ISR と追加したけれども、これは使っていない。
参考程度に PSoC Creater のプロジェクト
Download: hrtft-test.zip
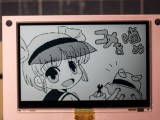
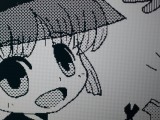
反射型LCDなので暗いところでは見えないけれども、明るいところでは割と細かいのと黒が深いのとでかなり綺麗に見える。
特に黒い部分は格子が見えにくくてベタに見えるので文字表示とかは良さそう。
書き換えはライン単位で、横400pixel = 50byte にコントロール 4byte を一気に送る手法。部分矩形の更新とかは面倒なので全画面書き換えっぽくなるんじゃないかなあ。
そして全画面書き換えようとすると 2MHz シリアルではそんなに早くないという印象。
モノクロで細かい LCDモジュールなのはうれしいけれども、1画面分のバッファを持とうとすると 50×240 で 12000byte が必要になってしまうため、非力なマイコンだと辛いかもしれないです。
フレキコネクタの入手性が悪いのと、フレキコネクタ実装のための基板をどうするかという問題が案外ハードル高いのでそこをどうするかでしょうな。
実際に表示できるようになると、おーと思うぐらい視認性が高く面白いモジュールなり。
posted by
rerofumi
2012/7/9 月曜日 3:35:52
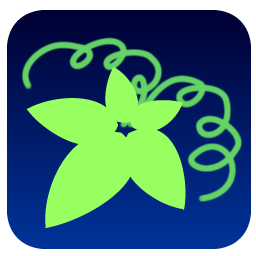
拙作の Gerber to G-Code アプリである Gynostemma だけれども「遅いよー」と常々言っているように処理に時間がかかるのが難点である。
高速化のために書き直すのもちょっと困難なので現状のままで提供している次第。
(そしてよくつっこまれる)
全面書き直しせずに ruby 版でもまだチューンの余地はあるのだけれども、その中でもマルチコア向けにマルチスレッド対応が常々やりたいと思っていたところ。演算のループやインスタンス構成をマルチスレッド用に改変しなくてはならないので手を出してこなかった。
IronRuby は .NET ベースなのでスレッドを使うと一応ネイティブスレットで駆動するようになる。パスの計算をマルチスレッド化すれば少しは早くなるのでは無いかといった目論見。
以下にマルチスレッド対応版を置いておく。
今回ちょっと大きく変わりすぎているのと検証が不十分なので「おためし版」としてのリリースとさせてもらう次第。問題があったら従来版に戻っていただきたい。
Download: gynostemma-20120709.zip (1.34MB)
Read the rest of this entry »
posted by
rerofumi
2012/6/30 土曜日 19:41:28
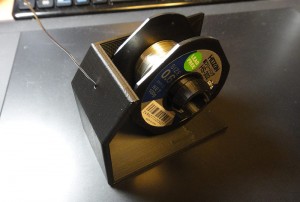
はんだリール台を 3Dプリンタで作ってみた。
斯様な小物は Thingivers でもメジャーなアイテムで、“solder” で検索するとはんだリールだけでもいくつか見つかる。
こういったアイテムを自作していくのが家庭用 3Dプリンターでの醍醐味であろう。
さて、今回はこの小物を作ったよというお話ではなく、それを作る過程のお話。
どんな 3DCAD を買って、使って作成をしようかということについて。
Read the rest of this entry »
posted by
rerofumi
2012/6/25 月曜日 4:04:59
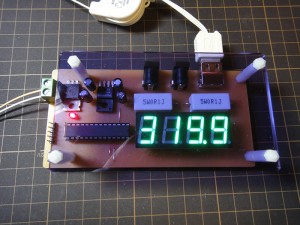
電子工作の試作や実験で使う電源のお話。
レギュレータで 5.0V と 3.3V を供給するBOXがあると便利かなと思って作ってみた。ついでなのでデジタル電流計もセットにしてある、どちらかというとこのデジタル電流計をつくってみたかったというのが一番の動機かも。
電子工作のさいに用いる電源としてメジャーなところとしては黒い色をした四角いACDCアダプタなのではないだろうか。特に秋月の小型スイッチング電源は多くの人が使っているんじゃないかと適当に推測する。
ACDCアダプタも良いのだけれども、あのジャックを毎回制作物につけるのが面倒だとか、5V以外の電圧を扱うようになったときとっかえひっかえが案外面倒だとかあるのです。特に取り違えは深刻で、うっかり12Vを食らわせてマイコンやLCDモジュールを破損させてしまったりするんですよ。これが。
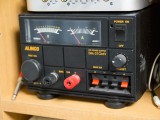
あるとき「直流安定化電源が欲しー」という発作に見舞われ、そのときにアルインコの無線機用電源を電子工作用に購入した。安くてそこそこの直流が得られるし、実験で電流が欲しいときにも 10A まで出力してくれる。
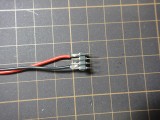
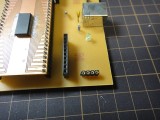
この電源装置から4ピンコネクタに電源を引いてきて使っていた。なので私が作る実験基板はいつも4ピンコネクタが電源となっていたのはそのせい。
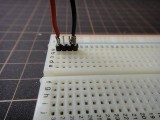
この形だとブレッドボードにもそのままさせるから案外便利なんだよ。
電源装置の方で 1~15V まで電圧可変できるので、必要に応じて調整していたがそのたびにテスターで計りながら合わせていた。それと接続ピンは写真の通りむき出しなのですぐ折れるのも問題であった。
3.3V と 5.0V の間を行き来することが多くなってきて、そのたびにテスターで見ながら合わせるのがだんだんと面倒になってきた次第。
そこで、5.0V と 3.3V の両方を出力する電源ステーションを作成することにした。
といっても面倒なことはなく、単に 5.0V と 3.3V 2つのレギュレータで電圧をそろえてジャックから出力するだけ。
それだけだと面白くないので、マイコンを使ったデジタル電流計をつけてみた。
電子工作中にプロダクトがどれくらいの電流を消費するかぱっとわかるようになるはず。
Read the rest of this entry »
posted by
rerofumi
2012/6/9 土曜日 22:12:52
CNCフライスを使ってのプリント基板自作を行う解説記事を書いてきましたが、予定の全12回全てを書き終えました。
ずいぶんと間が開きつつ時間がかかりましたがおつきあいくださりありがとうございました。
全12回分のインデックスを置いておきます
私がCNCフライスを手に入れ、プリント基板製作を行おうと思ったときに十分な情報とツールが無くて右往左往したものです。
そこからツールを自作し、目標とする QFP100 を含んだプリント基板の作成まで手探りでなんとかたどり着くことができました。
自分にとってやりたいことができるようになった今、振り返ってみると苦労していたあの頃とあまり状況は変わっておらず。製作手順に関するちゃんとまとまった資料がまだ無い様に思います。そこで、細かいところを含めながら私がプリント基板を自作している手順を書き起こしてみました。
これがそのまま通用するかというと使用するツールの違いなどから難しいと思いますが、取っかかりぐらいにはなるのではないかと思います。
また、今回記事としてまとめた意図として、なんだか盛り上がっているんだかいないんだかわからないけど話題にはなっている「電子書籍」を作って見たかったというもう一つの理由があります。
電子書籍の頒布とか販売とか試してみたくても、自分で書いた書籍が無いと何もできませんからね。
というわけで、これまでの全12回をまとめたものも以下に用意しています。
Download: PDF形式 fm-pcm_mil_20120609a.pdf
Download: ePub形式 fm-pcm_mil_20120609a.epub
まあ実際に電子書籍とするには装丁もイラストも足りませんが、気が向いたら足していきます。
ここまでで全23000文字ほどなので、一般的な書籍の 1/4 くらいのボリュームでしょうか。
書籍というより同人誌でまとめた方が良いくらいの分量かな。
ではでは、CNCフライスでみなさまの電子工作の世界が広がりますように。そしてこの記事がそのお手伝いとなりますように。
—–
追記
過去記事の「CNCフライスでプリント基板を作る動画」も併せてご参照ください。
posted by
rerofumi
20:38:00
第十二回『簡易2層を作成するには』
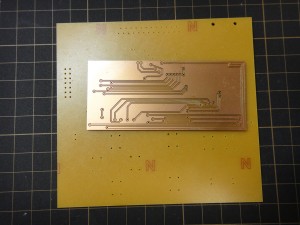
自作プリント基板で表面実装部品を扱うことが容易になりましたが、そのまま密度の高い実装へとシフトしていくと今度は片面基板で配線できないという状況になってきます。
少々であるなら部品面にジャンパー線をかける設計で解決できますがその数が多くなってくると二層基板がどうしても必要になってきます。
■ 貼り合わせ2層
自作基板で二層を作るというと一般的には両面銅箔板を両面ともエッチングなりの加工をして使うことをさしていました。両面銅箔板加工だと、表の加工と裏の加工で厳密に座標あわせをしないとビアの穴位置がずれてしまうという問題点があります。
その穴ずれはCNCフライスでのプリント基板加工でも同じ話であり、G-Code生成時の原点合わせや素材をひっくり返す際の原点合わせなど注意をしなければいけない場面がたくさんあります。簡単に言うと難しいのですね。
ひっくり返して両面加工というのを避けつつ、CNCフライスならではな二層配線の方法として加工した片面基板を2枚貼り合わせるという手法があります。
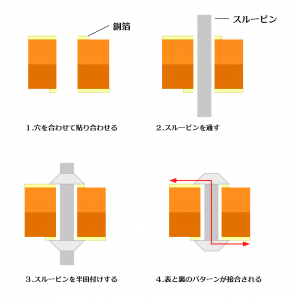
表の板と裏の板をそれぞれ別に作成し、双方をつなぐビア部分をスズメッキ線等のスルーピンを半田付けすることで接続するという作戦ですね。たくさんあるジャンパー線をプリント基板で代替するといったイメージの方が近いかもしれません。
スルーピンを設置するビアがたくさんあっても、穴が厳密でずれることが無いというのがCNCフライスならではのメリットですね。手作業穴あけのエッチング法ではこうはいきません。
基板を貼り合わせるので当然厚さは二倍になります。
通常 1.6mm 厚の銅箔板を使っているので貼り合わせたら倍の 3.2mm です。
これは厚すぎるというので半分の厚さである 0.8mm 厚の銅箔板も売られています。
ぱっと見良さそうなのですが、0.8mm 板は薄いため容易に反りが生じます。そのため扱いに注意が必要ですし、両面テープでテーブルに固定した後剥がすのにもそれなりな注意を払います。力をかけると曲がったり割れたりしてしまうんですよね。
なので 0.8mm は使いどころを考えて、あまり厚さを問わない通常の工作では 1.6mm 厚のまますすめる方が楽でやり良いです。
プリント基板製作会社に依頼して正式な二層基板を製造してもらうと、ビア(基板の穴)部分は銅箔メッキしてくれてそこはスルーホールになります。自作基板だとこのスルーホールができないのであくまで制限付きの簡易二層基板でしかないのは、制限と言えるでしょう。
ですがそれでもある程度の二層実装ができるだけで自作の可能性がグンと広がります。
Read the rest of this entry »
posted by
rerofumi
2012/6/7 木曜日 0:42:17
第十一回『基板の仕上げ』
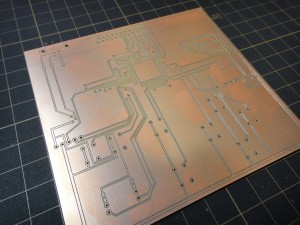
プリント基板の銅箔面はとても酸化しやすく、手の脂などが付いたところからみるみる変色していきます。
完成したプリント基板は磨いた後なんらかの方法で保護してあげましょう。
■ 洗浄
プリント基板が完成したら綺麗に洗浄をしましょう。
この過程はCNCフライスによるプリント基板製作だけでなく、エッチングで作成したプリント基板でも行います。
洗浄を行う理由は二つ。
一つは銅箔表面の酸化膜や油膜を削り落とすこと、そしてもう一つはフライスで切削した際の粉じんを溝から除去したり切削端のバリを削り落とすことです。
酸化膜は空気に触れているだけでできてしまうものですが、これをそのままにしておくと半田付けができないという問題もあります。
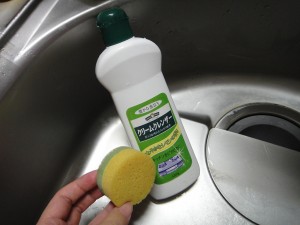
酸化膜除去のためにやすりで磨きましょうと紹介しているところもありますが、私は台所用クリームクレンザーの使用をお勧めしています。断然これです。百円ショップやスーパーで簡単に手に入りますので食器洗い用スポンジと一緒に買いそろえてください。メチャクチャ使えるプリント基板製作工具ですよ。
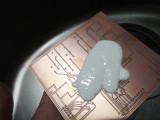
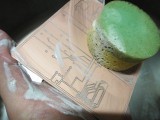
クリームクレンザーとスポンジでごしごしこすり落とすだけでピッカピカに仕上がります。
細かいくずもクレンザーとともに水で洗い流してください。
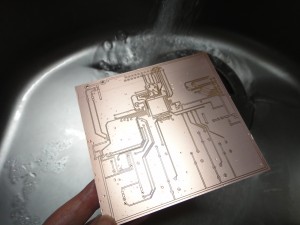
洗い終わったあとキムワイプで水気を拭き取るとちょっと玄人っぽくて悦に入ることができます。が、普通に布やティッシュでも十分です。
■ フラックスの塗布
洗い終わってぴかぴかの基板ですが、ほっておくと再び表面が酸化膜で覆われてしまうためになにかでコーティングしてやる必要があります。
プリント基板製作会社に依頼するとソルダーマスクで大部分覆われますし、露出している部分はハンダレベラー(半田を薄く塗布して銅箔を覆ってしまう)してくれますので安心です。
自作基板の場合、半田槽とかありませんので全面に手作業ハンダレベラーとかできません。
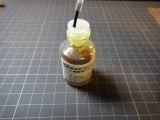
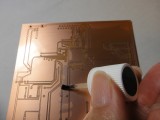
通常はフラックスを全面塗布して覆ってしまいます。フラックスは乾いてもべたべたするので埃とかくっついて汚くはなりますが、銅箔面の酸化は防いでくれます。それに半田付けのさいにフラックス本来の役目で半田の乗りを助けますので後々も便利です。
フラックスの塗布は刷毛でちびちび塗るのが良いです。スプレー式などもあるのですが綺麗に塗布するのが難しく、逆にムラとなってしまったりあまり良い印象がありません。
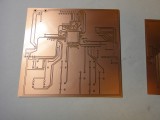
フラックスを塗り終わったら良く乾燥させてください。これで自作プリント基板の完成です。
posted by
rerofumi
2012/6/4 月曜日 0:21:08