posted by
rerofumi
2010/12/26 日曜日 18:01:11
CupcakeCNC は小型 3Dプリンターでもあるので製作できる形状は大きくはない。
なので、ある程度の大きさの物は分割して作成することになる。
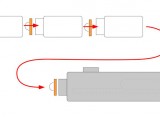
いるみさんでの分割プランはだいたいこんな感じ。
光るイルミネーション部分を接ぎ木できる様に設計し、間に LED基板を挟んでいくといった作戦。イルミネーション部分は白ABSで作って中身は空洞のままにするので、このジョイント部分が重要になっていく。
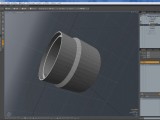
まずはジョイント部分のみのモデルを作成して実際に出力しながら合わせていく。
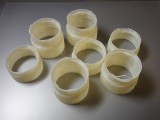
出力時の肉厚等実際に出力してみないとわからない部分もあって、CAD上での設計のみというわけには行かず何回も何回も出力して少しずつ合わせていくといった地味な作業。
実際には写真に写っている倍の量のテストプリントをしたと思う。
Read the rest of this entry »
posted by
rerofumi
2010/12/25 土曜日 16:50:38
エレキ部分が完成して動作もしたので、今度はその外側を覆い握りやすくするケースを作成する。
今回のプロジェクトの山は二つあって、一つがCNCフライスでプリント基板をつくること、もうひとつが CupcakeCNC でケースを作成すること。家庭用3Dプリンターでどこまでの物が製作できるのか、これまでに積み重ねた経験で完成させることができるか。どきどきの展開。
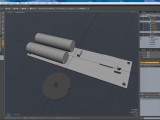
一番最初に行うのはエレキ部分の基板と部品のだいたいの形をモデルとして起こすこと。
この基板と部品のモデルを下書きとして、ぶつからないように外側をくるむケースを設計していくのです。
ノギスでサイズを測りつつ、モデラー上で数値入力しながらそこそこ厳密に外形を作っていく。
相変わらず CAD には慣れないので 3DCG のモデラーを使っている。モデラーは modo401 に乗り換えたばかりであまり慣れていないけれども、数値入力もやりやすいので特に問題無く作成できている感じ。
posted by
rerofumi
2:39:53
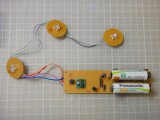
ここまででエレキ部分は完成。
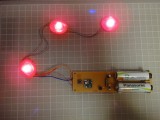
ちゃんと点灯もするよ。
ということで、こんどは安定して動作するかどうかのテストを行う。
満タンの電池で連続点灯して何時間くらい光っているかを見るのです。
と、これがなかなかうまくいかなくてですね。最初のトライでは 2時間で消えてしまいました。
ここで一週間ぐらいあーでもないこーでもないと調整をしていたのですが、結果としては LED ボード上になんらかの短絡があったらしくそれでダメになっていたという次第。
次に短絡を全て解消したら、今度は消えないもののやはり2時間くらいで点滅をはじめボタンでの色切り替えができなくなってしまうという現象が発生。これも原因究明が困難でしたが、マイコンからトランジスタスイッチを駆動させる手前で挟んでいる保護抵抗が小さすぎるというのが原因だった。
回路図ではすでに 470Ω に書き直してあるけれども当初ここは 100Ω だった。するとマイコンからのシグナルが大量に流れ過ぎでチャージポンプによる微弱な電流では貧血を起こしてしまっていたのですな。
わかってしまえばなんてことないけれども、調べているときはわかんなくてうんうん悩んでいたもの。
そういった不具合や調整もあらかた片付き安定したところで電池の電圧計測を行った。
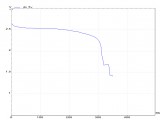
最も電力を消費する白色表示のときの電圧降下グラフ。ニッケル水素は 1本あたり 1V 以下まで使うとよろしくないらしいので、2V 未満は使わない方が良い領域。といってもその近傍ではストンと電圧がさがるのですぐに LED が消えると思う。
1.7V で一回棚ができているのは LEDドライバーが駆動しなくなり LED が消えたため、消費電流が押さえられたのだと思う。
で、この計測結果をみると 5時間30分が駆動時間になるらしい。
要求の 6時間にはちょっと足りないけれども、まあぎりぎり許容の線。
別の色にしていると消費電流が下がるので、6時間は超えるはず。
posted by
rerofumi
2010/12/23 木曜日 16:46:05
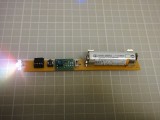
プリント基板を作るために四苦八苦した「いるみさん」プロジェクトですが、一回できてしまうと私的には非常にたやすく基板作成ができるようになります。
そんな状況になったことで調子ぶっこいて、電池一本で駆動する小型版をオマケで作成することにしました。yytuneさんのコンサートライトを PSoC で別実装したような感じになります。
使用する PSoC は 8pin の CY8C27143。電池1本から 3.3V に昇圧するのにはやはりストロベリーリナックスのDCDCモジュールAS1322A を用意しています。
パワー指向の「いるみさん」と違って、マイコンと LED 両方の電圧を 1つの DCDC でまかなっていますので大電流が取れず制限抵抗も必要となることからあまり明るくはできません。
そこそこの明るさのものを安定して作るというのが mini の役割となります。
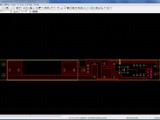
基板設計。
今回はオマケなので本当に回路図もなにもなくいきなりパターンを書いています。
Download: irumi_mini_garber_20101223.zip
ガーバーを出力して。
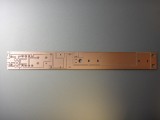
プリント基板を作って。
Download: psoc_irumi_mini_20101223.zip
ファームはいるみさんのを流用して。
で、完成。
1日でできる作業でした。
Read the rest of this entry »
posted by
rerofumi
2010/12/22 水曜日 1:00:51
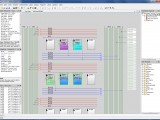
マイコンに書き込むファームウェアの作成。
個人的に悩むことのないフェーズなのでプロジェクトファイルをぽこっと置いて終わりにしておく。
Download: led_irumi_20101221.zip
設計としては、PSoCのデジタルブロックを使って 3つの 8bit PWM モジュールを置き、それで LED の明度を指定している。なので MPU はその PWM モジュールに数字をセットするだけの役割でボタン監視ぐらいしか行っていない。
16bit のカウンターはウェイトタイマー用に 16ms 間隔での割り込みを発生させるためのもの。キーチャタリング防止とか、時間計測とかに使っている。
機能としては、ボタンでプリセットの色が変わっていき、ボタン長押しでじんわり色が変わるレインボーモードになるとか、ボタンを押しながら電源ONで点滅モードとか仕様通り。
posted by
rerofumi
2010/12/20 月曜日 23:36:00
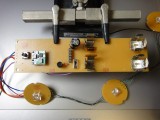
いわゆるひとつのはんだ付け作業。
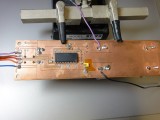
プリント基板さえ作れば、はんだ付けは簡単なお仕事。そう考えていた頃がおれにもありました……
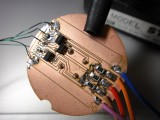
簡単になるのはスルーホールのDIP部品だけじゃんかよ。表面実装はソルダーマスクがないとブリッジしまくるしまくる。
まあ、溝が 0.27mm しかないから当然かもしれないけれども。
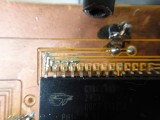
ルーペで見ながらはんだ付けして、一個つける毎にテスターでショートしていないかをチェック。はんだ吸い取り線が大活躍しつつ、ヒーヒーいいながらなんとか実装を終えたのでした。
posted by
rerofumi
2010/12/19 日曜日 16:02:23
プリント基板のガーバーデーターができたら、それをフライスで削り出すための GCODE に変換する。
ここがうまくいかなくて悩んだ末に変換ツールを作ったというのがこれまでに語ってきたお話。
まず、ガーバーは太さ情報(プロッターのシャッターサイズ)を持ったデーターなのだけれども、GCODE は軌道情報のみという違いがある。ガーバー自体も GCODE の亜流なのだけれども、そのまま変換するとパターンの中心にそって線を一本掘るだけの結果となる。
なのでまず、太さ情報と軌道情報からパターンの外周を算出して表示する必要がある。これがガーバービューアのお仕事。
次に、フライスで切削するには刃のサイズを考慮しなければならない。例えば直径 1mm のカッターで切削していった場合、刃の半径サイズ分 5mm 外周より内側にめりこんでちょっと小さく削ってしまうことになる。当たり前の話だけれどもこれを回避するために実際に刃を移動させる軌跡は外周の軌道情報から刃サイズの半分だけ外側を縁取るように拡張しなければならない。
その拡張をどうやるかが難しかった。
理屈から言ってパターンだけでなく外形にも刃サイズ分の拡張を適用しないといけないのだけれども、今回は難しかったので外形については無視することにした。
あらかじめ CAD 上で外形サイズを刃サイズ分だけ大きくしておくという運用での回避でごまかすのだ。
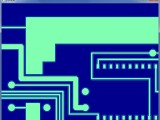
マイコンボードのガーバーを GCODE 変換。
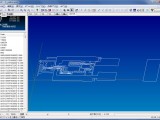
NCVC でパターン切削の GCODE を確認。
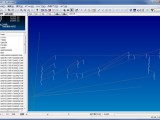
ドリルデーター。
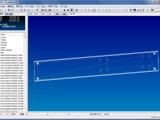
外形くりぬきデーター。
こうしてできた GCODE でCNCフライスを駆動し、銅箔紙フェノール板を削ることでプリント基板が完成する。
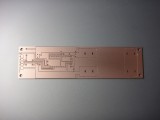
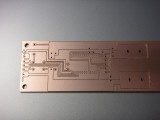
これくらいのものがざくざく自作できるようになってくると、もう楽しくて仕方がない。
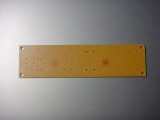
穴開けに苦労しなくていいなんて夢のようでござる。
これと以前作った LED 基板と合わせて、いるみさんのプリント基板は完成。
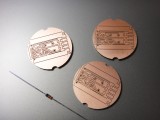
posted by
rerofumi
2010/12/14 火曜日 23:34:18
特に語ることもなく、K2CAD で黙々とプリント基板を作る。
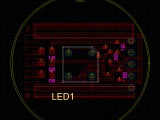
こちらがすでに何度か出てきている LED ボード。
3色 LED とスイッチ用の表面実装トランジスタ、必要ならば制限用にチップ抵抗を取り付けられる。それを丸い形のプリント基板にするあたりがポイント。
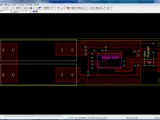
PSoC とDCDCを乗せたコントロール基板、電源であるニッケル水素電池のサイズから外形が決まっている感じ。
電池金具の穴は外形レイヤーにつけてある。外形を 1mm のエンドミルでくりぬく際に、金具穴も開けてしまおうという魂胆。1mm という幅がちょうど良い感じなので。
上記二枚のガーバーデータ。レイヤーは、ソルダーパターン/外形/ドリル穴 の 3枚。
Download: irumi_garber_20101214.zip
CADデータを置いても良いんだけれども K2CAD なんだよな。使っている人いるのかなん。
posted by
rerofumi
0:51:24
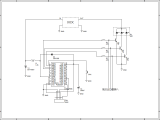
電子工作部分の回路図はこんな感じ。
って、実は回路図引かずに直接基板設計してたからこれは事後に書き起こしたもの。
最初はプッシュスイッチにプルアップをつけていたけれども、実装時は PSoC 内のプルアップ回路を利用する事にしたから外したとか。ごにゃごにゃあって部品の値を変えたりとか細かい変更があった程度かね。
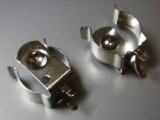
秋月で買った電池金具。
これを基板につけることで電池を実装する。というあたりを規定としてプリント基板の設計へ入っていくのでした。
posted by
rerofumi
2010/12/12 日曜日 17:14:49
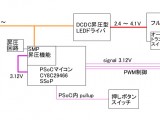
電源周りに注目したブロック図をざっくりと書いてみた。
ニッケル水素電池からの出力をマイコン用の昇圧回路とLED用の昇圧回路のそれぞれにわけて与えているところが今回の中心。定電圧が必要なマイコンと、電流次第で電圧が変動するLEDは分けておこうというお話。
LEDドライバーはLED専用なので制限抵抗無しでダイレクトにLEDを駆動できる。このため抵抗を追加する必要がなくて、余計な電力を食わずにすむはず。
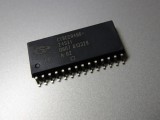
マイコンは PSoC CY8C29466 の面実装パッケージ。以前 DigiKey で買った在庫がまだ手元にあったのでそれを使用。
PSoC でSMP(昇圧ポンプ機能)がついている奴って 28pin のになっちゃうのよね。
面実装部品を使おうと思えるのも、自分でプリント基板を作るからなのです。