posted by
rerofumi
2012/5/27 日曜日 23:16:40
第九回『パターンの切削』
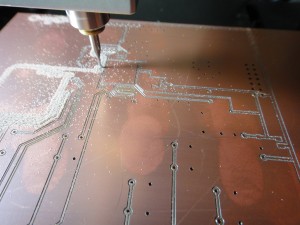
■ 基板カッターによる切削
プリント基板加工最大の特徴&山場であるパターンカッターによる切削です。
最大の特徴という割には特殊な事はあまりありません。一番の特徴は基板加工用のV字カッターを使うくらいでしょうか。
昔は半月V字カッターを研いで使うなどが一般的でしたが、現在ではオリジナルマインドさんの基板加工用カッターである「美濃昌典」「土佐昌典V」を使うのが良いと思います。多少お値段が張っても切れ味の良さには変えられませんので。
V字カッター以前ではできるだけ細いエンドミル(0.5mm程度)のものを使っていた様なのですが、あまり細かい精度が出ない上に良く折れていたそうです。
現在の 0.25mm 幅でパターンが彫れるというのは、それなりに進歩した結果なのですね。
■ 注意点
パターン切削の注意点は「銅箔面を水平に保つ」最初から最後までこれにつきます。
パターン切削はフライスの刃で銅箔面を薄く剥いて絶縁させることで作っていきます。V字型のカッターは先端がとがっている事から、浅く削れば細く、深く削れば太く掘る事ができます。
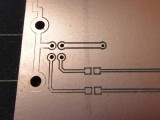
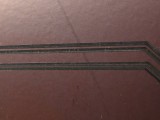
そのため、銅箔板が水平になっていないと刃が浮いてパターンが途切れたり、逆に沈んで太く掘ってしまいパターンが無くなってしまったりということになります。あくまで銅箔面のどこでも同じ太さになるようにしなければいけません。
市販されているプリント基板加工用のV字カッターは表面から 0.1mm の深さで切削する事を想定して作られている様です。どこでも 0.1mm の深さで掘れるというのは案外難しく、目に見えない反りや傾きで容易に失敗してしまうものです。
個人的な経験から、プリント基板のパターン切削にはクランプ固定は適していないと思います。
両面テープを加工領域全域にまんべんなく張りつけ、均等な厚さで貼り付けるのが
もちろんそのときに傾いたりしないように、両面テープが折り返していたりゴミを巻き込んで厚さが不均等になっていたりしないよう最善の注意をする必要があります。
■ カッターが切れなくなるとどうなる?
基板加工カッターも刃物ですのである程度使ってくると切れ味が鈍ってきます。
半月V字カッターの頃は自分で研ぎ直すというのも良く行われていましたが、2枚刃の奴は磨げるのでしょうか?個人的には試したことはありませんし、なんだか上手くいかなそうで怖じ気づいています。
その基板加工カッターを実際に使い込んでいき切れなくなるとどうなるかですが、これは掘ったパターンの後、カットのサイドに「バリ」が現れ始めます。刃の切れが悪くなるほどにバリの量が増えていく感じです。なので加工後基板表面を素手で撫でてバリがあるかどうかを確認してみてください。
切れなくなってバリが出るのにまだ使い続けているとどうなるかというと、これが先端の刃がぽっきりと折れてしまいます。
彫れないのに進む力は一定なので、横方向に力がかかるようになりポキッといってしまうのですね。
折れたら寿命だと刃を交換するのも良いのですが、その直前で新しい刃に変えた方が精度の高い工作が続けられることでしょう。
「美濃昌典」でどれくらいの寿命があるのかというと、大体 150x100mm サイズの銅箔面を 10枚つかったあたりで1本といった所ですかねえ。
1本3480円+板1枚180円×10 = 5280円がランニングコストなのですが、それでも自作基板の魅力と天秤にかけるとお安い方では無いかと思うのです。
posted by
rerofumi
2012/5/19 土曜日 14:10:13
第八回『ドリルで穴あけ』
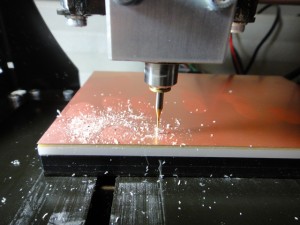
実際にCNCとG-CODEで加工を始めましょう。まずは穴開けからです。
パターン堀りとドリル穴のどっちが先かは特に論ずるほどの事は無いのですが、パターンを掘った後の銅箔は非常に細く剥離しやすいため「後ドリル」はなんだか怖くて「先ドリル」にしています。
■ 穴の深さと捨て板
CNCフライスでの穴開けは、刃を回転させた状態で Z軸を下方向(素材にめり込む方向)へ移動させることで行います。
素材の表面がゼロ地点な訳ですから、穴を掘り進めたい深さだけ Z軸を移動させることとなります。
角形のエンドミルならば掘り下げた距離がそのまま穴の深さになるので、板の厚みと同じ数値掘り下げるでも穴を空けることができます。ですが、一般的なドリル刃は先端がとがったV字になっているため板の厚みと同じだけ掘り下げても穴が貫通しない事になります。
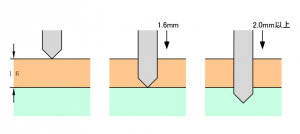
そのため、ドリルで穴を空けるためには板の厚さより多く掘り下げて意図的に貫通させてやる必要があるのです。
私が 1.6mm のプリント基板に穴を空けるときはいつも 2.0mm ほどの掘り下げ量に設定しています。
それだけ掘り下げて貫通させるということは素材の下もある程度掘るということになります。なので、加工時には必ず捨て板が必要になるわけです。
■ ツールごとに穴あけ
個人用の卓上フライスでは「自動ツールチェンジャー」なる便利なモノは搭載されていませんから、加工内容によって刃を取り替えてやる必要があります。
Gynostemma ではドリル径毎に別々の G-Code を出力しますので、ドリル刃をセットして G-Code を読み込ませ加工、次のドリル刃をセットして G-Code を読み込ませ加工、といった作業を繰り返してやる手順となります。
刃を交換したら必ず Z軸のゼロ点出しを行うことを忘れないでください。
これを忘れてしまうと、素材にめり込んだ状態のまま移動しようとしたりして素材だけで無く刃もおってしまうことになります。
これまでに何本折ったことか……。
■ ねじ穴はどうするか
ねじ穴やパーツの固定穴で M3 や M2 といった大きな穴が必要になるときがあります。
2.2mm や 3.2mm といったドリル刃を用意すれば良いのですが、フライス用のドリル刃は高価で入手法も限られています。
ある程度大きな穴であれば以下のどちらかの方法で空けるのが良いでしょう。
- 一旦 1.0mm 程度の細いドリル刃で穴を空けておき、後から手作業でドリルして目的径の穴にする
- 1.0mm とか適度な幅のエンドミルで円を描いて目的径の穴にする
CNCフライスの作業っぽいのは後者の方ですが、穴が少ない場合は前者の方が簡単で手っ取り早いときもあります。
エンドミルで穴をあけるのは外周切り抜きの時に一緒にやると良いでしょう。
posted by
rerofumi
2012/5/15 火曜日 23:03:51
第七回『基板切削の準備』
CNCフライスで切削を始める前に準備をしましょう。
■ 捨て板
プリント基板として切削する銅箔板のほかに、一緒に切ったり穴を空けたりしても良い板を用意しておきます。これを捨て板といいます。
ボール板などで穴を空けるときに、穴を空けたい素材の下に木板などをおいて一緒に穴開けをしますがそれと同じ意味を持ちます。穴あけ時の貫通面破損を押さえる効果と、突き抜けて加工する穴あけ掘削時にテーブルを傷つけない様にといった用途で用います。
オリジナルマインドさんの作例を見ていると銅箔板と捨て板を毎回セットで貼り合わせて使い、捨て板も一回の加工で捨ててしまうようですね。確かにそれは確実な使い方という気がします。
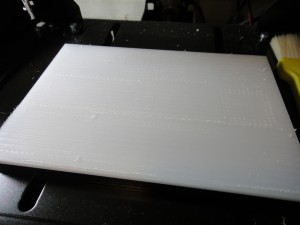
私はテーブルの上に POM の板を一枚張って、それを捨て板として使っています。
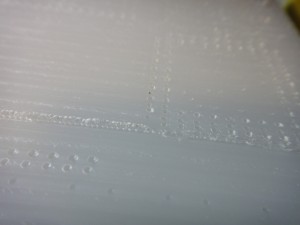
実際にプリント基板を作った後では、ドリルの穴や基板切断時の溝などが残ります。
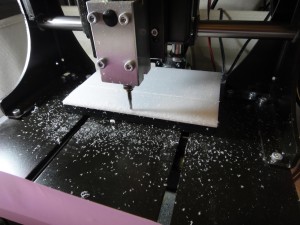
ある程度表面がぼろぼろになって使いにくくなったら、面だしコードで表面を薄く削ります。
これで穴の開いていない面が用意できるのでまたきれいな切削が行えます。
少しずつ少しずつ削って使える面を作っていくので、数ミリの POM で結構持ちます。
1.6mm のベークライト板を使っていたこともありましたが、0.2~0.4mmずつ削っても数回使えるので割と長持ちしました。
■ 両面テープ
CNCフライスのテーブルに固定ねじやクランプがあればそれで銅箔板を固定します。
無い場合は両面テープで銅箔板をテーブルや捨て板に固定することになります。
プリント基板の場合は張り付きやすいので両面テープの利用で良いのでは無いかと思います。
その際両面テープの選択が結構重要になります。
強力なテープを使ってしまうと加工が終わった後剥がせなくなってしまいますし、無理に剥がそうとして曲げてしまったり割ってしまったりする可能性が出てきます。
かといって剥がしやすいテープを使うと、今度は加工中に剥がれて失敗してしまう可能性があります。
どんなテープが良いかというとむずかしいのですが、私は基材が紙じゃ無いものを推します。
紙が基材の両面テープは破けやすいので、加工後剥がすのに大変苦労します。
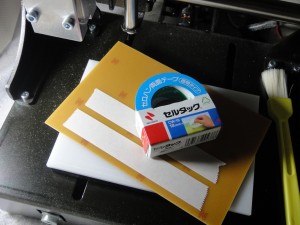
一押しは「セルタック」というセロハンテープ基材の奴なのですが、入手しにくいという難点があります。
■ ゼロ点出し
これは基材準備ではないのですが、CNCソフト上でここを工作の原点としようというゼロ点決めを行う必要があります。
Gynostemma ではパターン切削、ドリル穴あけ、外形切削の 3種類の G-Code を出力しますが、これらのXY原点は全て同じとしています。なので、最初にここをXY原点として設定するよと決めたらツール(刃)を交換しても触らずにそのまま最後まで使い続けます。
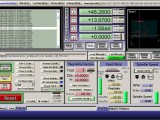
通常はCNCソフトにゼロリセットボタンがあり、押すと座標がゼロにリセットされ現在の刃の位置が原点となります。
Z軸縦方向のゼロ点は刃のセット位置によって微妙に変化します。
Z軸のゼロ点だしについては、刃の止めねじを緩め落下させ板にコツンと当たって止まったところをゼロとします。そこでねじをとめてCNCでZ軸の座標をゼロにリセットします。
プリント基板については板の上なのでこのゼロ点出しの方法で十分事足ります。
これは刃を替える毎に毎回やる必要があります。できるだけ平らな面の上に刃を持って行ってそこでゼロ点だしを行いましょう。
posted by
rerofumi
2012/5/7 月曜日 1:20:29
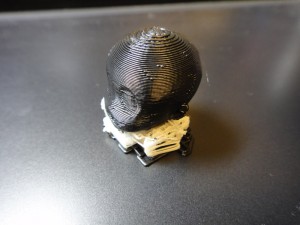
前回の記事にて、Makerbot replicator の2色出力を応用して PVA によるサポート付きの立体出力ができたことをリポートした。
これは原理実験であり、できることがわかったというお話。
じゃあ実用とするのに、どうやってサポート出力をしようかという問題が残っている。
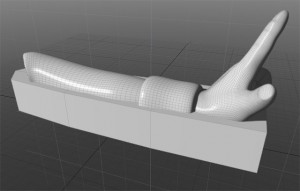
毎回毎回この様にサポート形状を作成するのは正直面倒である。
面倒なだけならまだ良いが、メッシュ系のポリゴンモデラーだとブーリアンで型を抜くのがあまりうまくいかないのよね。修正なしの一発でとはいかない。
なのでどうやってサポートを出力させようかというのは考えどころとなる。
Read the rest of this entry »
posted by
rerofumi
2012/5/6 日曜日 23:35:22
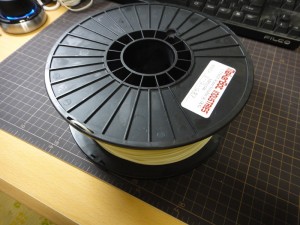
2012年の GW はなんだか雨模様で残念な関東でございましたが、そんな雨の日が続いていたせいか 3Dプリンター用の PVA フィラメントが「湿気って」いた。
水に溶けるものなので、湿気るのは想定内ではあるんだけれども思ったより早いなーというか。ビスケットやせんべいと同じ扱いをしないと駄目なのか。
湿気ってふにゃふにゃ柔らかくても一番懸念していたフィーダーでの巻き取りも問題なくて、replicator での出力も問題無いかと思っていたのだけれどもやっぱり色々と残念な感じに。
リールにある全てが湿気っているのでそっちが重くなって絡みやすくなっていた。おかげでモーターが引っ張っても重たい&引っかかりやすくて途切れるパターン。
あと、steptluder のモータが押し出した後、ヒーターまでの間にちょっと隙間があるのだけれども、そこに押し込む力がかけられずふにゃんと曲がって端から出てくる始末。
ある程度の堅さがないと押し出したあと色々と不都合のようだ。
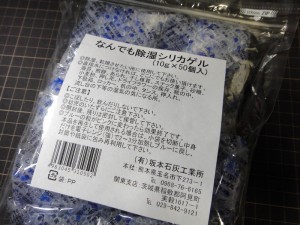
とりあえずシリカゲル買ってきて袋に一緒に放り込み密封してみた。
使えるまで復活するといいな。
posted by
rerofumi
2012/5/5 土曜日 21:59:06
第六回『刃(ツール)の種類』
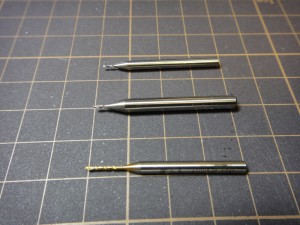
CNCフライスでは目的の加工に応じて色々な種類や大きさの刃を利用します。
ここではプリント基板作成に使う刃を見ていきましょう。
■ エンドミル
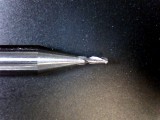
エンドミルはCNCフライスで通常使われる刃です。
刃先の形状が丸いボール型と、矩形になっている角形の2種類が一般的です。
上記写真の刃は角形1mm径のものです。
角形は一番下の底面と側面のそれぞれに刃が有り、ここにふれたものを全て削り飛ばします。側面でも切削できるので、素材に突き刺して横にずいーっと移動すれば切断になるのですね。
プリント基板作成では主に基板の切り抜きとねじ穴の様な大きな穴開けに使います。
カッティングに使う分には径が小さいほど幅が小さく刃サイズを意識しなくて済みそうなところですが、細いと高い上に折れやすいので 1mm あたりの廉価セットが一番お得に使える気がします。
通常のエンドミルは金属加工も視野に入れているのですが、プリント基板で使う紙フェノール(ベークライト)はそれに比べて十分に柔らかいので最適というわけでもないようです。樹脂やアルミといった柔らかい素材専用のエンドミルも存在し、それを使うと幾分静かに切削できるようです。
ただ、樹脂用エンドミルは若干お高めで、効果抜群とまではいかないので費用対効果としては通常の廉価エンドミルで十分ではないかと思います。
■ ドリル
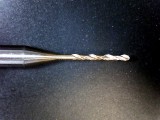
おなじみのドリル刃です。
金属に穴開けするわけでも無いので特筆することもないのですが、CNCフライスのスピンドル(後述)にセットできる径である必要があるのでCNCフライス専用のドリル刃となります。ホームセンターで売っているドリルの刃を買ってきてセットできるわけではありません。
取り付けの軸径は大体 3mm のものが多い様です。
刃の径は必要に応じて揃えてください。
私は以下の3種類を揃えて使いわけています
- 0.8mm 通常の DIP ホール
- 1.0mm ピンヘッダ等のコネクタで使う
- 0.6mm 2面貼り合わせのスルーピン用ホール
■ PCBカッター
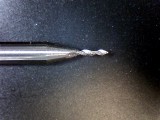
プリント基板のパターンを掘るための刃です。
大体 0.2~0.4mm 幅の溝を掘ることを目的としています。
通常は先端がV字型をしており、基板にめり込ませる深さで切削幅を調整します。カット基板の銅箔の厚さは 35μm くらいなので 0.1mm も下げれば十分に切断できます。
写真の刃はオリジナルマインドの「美濃昌典(先端53度)」です。ちょうどエンドミルの先端を細めたような形をしていますし、0.8mm径のドリルとしても使えます。
先端53度というのは、深さ 0.1mm に沈めたとき切削幅が大体 0.2mm 近くになるという設計の様です。
■ コレット
CNCフライスでは回転するスピンドルの部分に刃をセットするのですが、このスピンドルの穴の径で使える刃がきまります。
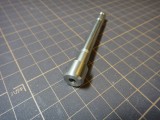
スピンドルに刃を差し込んで芋ねじで固定するのですが、スピンドルの径ちょうどの刃を使わないといけません。しかし、刃によってこの径が 6mm, 4mm, 3.175mm, 3mm と様々です。(iModela はハンドリューターサイズの2.35mm)
刃の軸径に合わせてスピンドルを用意しそれを差し替えるのが推奨されている使い方となります。
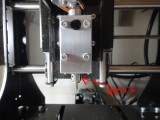
しかし、スピンドルはスピンドルホルダーに取り付けられフライスに固定されているため、交換するにはZ軸をほとんどばらしてまた組み立てるという作業が必要になってしまいます。
そこで私は径変換のスリーブコレットを利用しています。
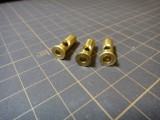
コレットを使うと偏心する可能性があるため推奨ではないのですが手軽に径の違った刃を交換できるようになります。
私はキデッジショップさんで購入したのですが、現在は在庫なしになっているようですね。探してみると同様のコレット(もしくはスリーブという名称)で扱っているところがいくつか見つかりますのでそういったところで在庫があるところから買い求めるとよいのではないかと思います。
今使っている刃だと、ドリルと美濃昌典が 3mm 軸、エンドミルが 4mm 軸なのでこの二種類があれば事足りている次第。
オリジナルマインドさんは、この軸の違いを考慮してできるだけ1本の刃で交換なしに仕上げるようにという方針の様子。「土佐昌典」シリーズはそういうコンセプトの刃。これだとスピンドル径が一つで済むからね。
他の刃を使いたい、特にエンドミルを使うところをどうにかすれば 3mm 軸一本で済ますことができるかもしれません。