posted by
rerofumi
2012/5/19 土曜日 14:10:13
第八回『ドリルで穴あけ』
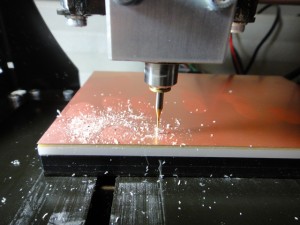
実際にCNCとG-CODEで加工を始めましょう。まずは穴開けからです。
パターン堀りとドリル穴のどっちが先かは特に論ずるほどの事は無いのですが、パターンを掘った後の銅箔は非常に細く剥離しやすいため「後ドリル」はなんだか怖くて「先ドリル」にしています。
■ 穴の深さと捨て板
CNCフライスでの穴開けは、刃を回転させた状態で Z軸を下方向(素材にめり込む方向)へ移動させることで行います。
素材の表面がゼロ地点な訳ですから、穴を掘り進めたい深さだけ Z軸を移動させることとなります。
角形のエンドミルならば掘り下げた距離がそのまま穴の深さになるので、板の厚みと同じ数値掘り下げるでも穴を空けることができます。ですが、一般的なドリル刃は先端がとがったV字になっているため板の厚みと同じだけ掘り下げても穴が貫通しない事になります。
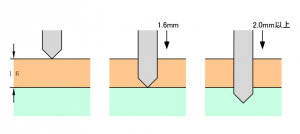
そのため、ドリルで穴を空けるためには板の厚さより多く掘り下げて意図的に貫通させてやる必要があるのです。
私が 1.6mm のプリント基板に穴を空けるときはいつも 2.0mm ほどの掘り下げ量に設定しています。
それだけ掘り下げて貫通させるということは素材の下もある程度掘るということになります。なので、加工時には必ず捨て板が必要になるわけです。
■ ツールごとに穴あけ
個人用の卓上フライスでは「自動ツールチェンジャー」なる便利なモノは搭載されていませんから、加工内容によって刃を取り替えてやる必要があります。
Gynostemma ではドリル径毎に別々の G-Code を出力しますので、ドリル刃をセットして G-Code を読み込ませ加工、次のドリル刃をセットして G-Code を読み込ませ加工、といった作業を繰り返してやる手順となります。
刃を交換したら必ず Z軸のゼロ点出しを行うことを忘れないでください。
これを忘れてしまうと、素材にめり込んだ状態のまま移動しようとしたりして素材だけで無く刃もおってしまうことになります。
これまでに何本折ったことか……。
■ ねじ穴はどうするか
ねじ穴やパーツの固定穴で M3 や M2 といった大きな穴が必要になるときがあります。
2.2mm や 3.2mm といったドリル刃を用意すれば良いのですが、フライス用のドリル刃は高価で入手法も限られています。
ある程度大きな穴であれば以下のどちらかの方法で空けるのが良いでしょう。
- 一旦 1.0mm 程度の細いドリル刃で穴を空けておき、後から手作業でドリルして目的径の穴にする
- 1.0mm とか適度な幅のエンドミルで円を描いて目的径の穴にする
CNCフライスの作業っぽいのは後者の方ですが、穴が少ない場合は前者の方が簡単で手っ取り早いときもあります。
エンドミルで穴をあけるのは外周切り抜きの時に一緒にやると良いでしょう。
posted by
rerofumi
2012/5/15 火曜日 23:03:51
第七回『基板切削の準備』
CNCフライスで切削を始める前に準備をしましょう。
■ 捨て板
プリント基板として切削する銅箔板のほかに、一緒に切ったり穴を空けたりしても良い板を用意しておきます。これを捨て板といいます。
ボール板などで穴を空けるときに、穴を空けたい素材の下に木板などをおいて一緒に穴開けをしますがそれと同じ意味を持ちます。穴あけ時の貫通面破損を押さえる効果と、突き抜けて加工する穴あけ掘削時にテーブルを傷つけない様にといった用途で用います。
オリジナルマインドさんの作例を見ていると銅箔板と捨て板を毎回セットで貼り合わせて使い、捨て板も一回の加工で捨ててしまうようですね。確かにそれは確実な使い方という気がします。
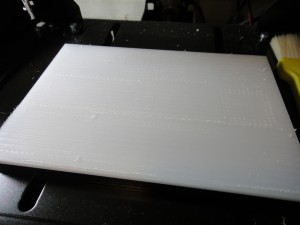
私はテーブルの上に POM の板を一枚張って、それを捨て板として使っています。
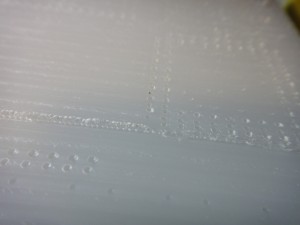
実際にプリント基板を作った後では、ドリルの穴や基板切断時の溝などが残ります。
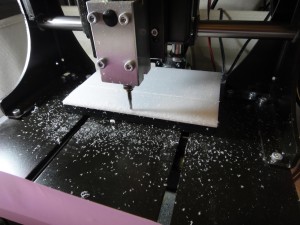
ある程度表面がぼろぼろになって使いにくくなったら、面だしコードで表面を薄く削ります。
これで穴の開いていない面が用意できるのでまたきれいな切削が行えます。
少しずつ少しずつ削って使える面を作っていくので、数ミリの POM で結構持ちます。
1.6mm のベークライト板を使っていたこともありましたが、0.2~0.4mmずつ削っても数回使えるので割と長持ちしました。
■ 両面テープ
CNCフライスのテーブルに固定ねじやクランプがあればそれで銅箔板を固定します。
無い場合は両面テープで銅箔板をテーブルや捨て板に固定することになります。
プリント基板の場合は張り付きやすいので両面テープの利用で良いのでは無いかと思います。
その際両面テープの選択が結構重要になります。
強力なテープを使ってしまうと加工が終わった後剥がせなくなってしまいますし、無理に剥がそうとして曲げてしまったり割ってしまったりする可能性が出てきます。
かといって剥がしやすいテープを使うと、今度は加工中に剥がれて失敗してしまう可能性があります。
どんなテープが良いかというとむずかしいのですが、私は基材が紙じゃ無いものを推します。
紙が基材の両面テープは破けやすいので、加工後剥がすのに大変苦労します。
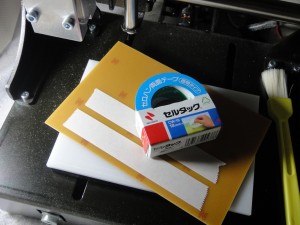
一押しは「セルタック」というセロハンテープ基材の奴なのですが、入手しにくいという難点があります。
■ ゼロ点出し
これは基材準備ではないのですが、CNCソフト上でここを工作の原点としようというゼロ点決めを行う必要があります。
Gynostemma ではパターン切削、ドリル穴あけ、外形切削の 3種類の G-Code を出力しますが、これらのXY原点は全て同じとしています。なので、最初にここをXY原点として設定するよと決めたらツール(刃)を交換しても触らずにそのまま最後まで使い続けます。
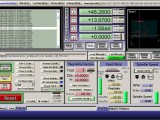
通常はCNCソフトにゼロリセットボタンがあり、押すと座標がゼロにリセットされ現在の刃の位置が原点となります。
Z軸縦方向のゼロ点は刃のセット位置によって微妙に変化します。
Z軸のゼロ点だしについては、刃の止めねじを緩め落下させ板にコツンと当たって止まったところをゼロとします。そこでねじをとめてCNCでZ軸の座標をゼロにリセットします。
プリント基板については板の上なのでこのゼロ点出しの方法で十分事足ります。
これは刃を替える毎に毎回やる必要があります。できるだけ平らな面の上に刃を持って行ってそこでゼロ点だしを行いましょう。
posted by
rerofumi
2012/5/5 土曜日 21:59:06
第六回『刃(ツール)の種類』
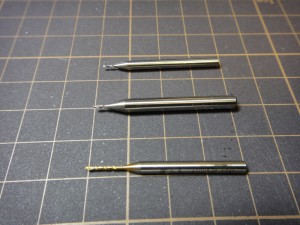
CNCフライスでは目的の加工に応じて色々な種類や大きさの刃を利用します。
ここではプリント基板作成に使う刃を見ていきましょう。
■ エンドミル
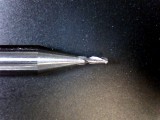
エンドミルはCNCフライスで通常使われる刃です。
刃先の形状が丸いボール型と、矩形になっている角形の2種類が一般的です。
上記写真の刃は角形1mm径のものです。
角形は一番下の底面と側面のそれぞれに刃が有り、ここにふれたものを全て削り飛ばします。側面でも切削できるので、素材に突き刺して横にずいーっと移動すれば切断になるのですね。
プリント基板作成では主に基板の切り抜きとねじ穴の様な大きな穴開けに使います。
カッティングに使う分には径が小さいほど幅が小さく刃サイズを意識しなくて済みそうなところですが、細いと高い上に折れやすいので 1mm あたりの廉価セットが一番お得に使える気がします。
通常のエンドミルは金属加工も視野に入れているのですが、プリント基板で使う紙フェノール(ベークライト)はそれに比べて十分に柔らかいので最適というわけでもないようです。樹脂やアルミといった柔らかい素材専用のエンドミルも存在し、それを使うと幾分静かに切削できるようです。
ただ、樹脂用エンドミルは若干お高めで、効果抜群とまではいかないので費用対効果としては通常の廉価エンドミルで十分ではないかと思います。
■ ドリル
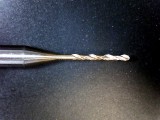
おなじみのドリル刃です。
金属に穴開けするわけでも無いので特筆することもないのですが、CNCフライスのスピンドル(後述)にセットできる径である必要があるのでCNCフライス専用のドリル刃となります。ホームセンターで売っているドリルの刃を買ってきてセットできるわけではありません。
取り付けの軸径は大体 3mm のものが多い様です。
刃の径は必要に応じて揃えてください。
私は以下の3種類を揃えて使いわけています
- 0.8mm 通常の DIP ホール
- 1.0mm ピンヘッダ等のコネクタで使う
- 0.6mm 2面貼り合わせのスルーピン用ホール
■ PCBカッター
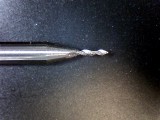
プリント基板のパターンを掘るための刃です。
大体 0.2~0.4mm 幅の溝を掘ることを目的としています。
通常は先端がV字型をしており、基板にめり込ませる深さで切削幅を調整します。カット基板の銅箔の厚さは 35μm くらいなので 0.1mm も下げれば十分に切断できます。
写真の刃はオリジナルマインドの「美濃昌典(先端53度)」です。ちょうどエンドミルの先端を細めたような形をしていますし、0.8mm径のドリルとしても使えます。
先端53度というのは、深さ 0.1mm に沈めたとき切削幅が大体 0.2mm 近くになるという設計の様です。
■ コレット
CNCフライスでは回転するスピンドルの部分に刃をセットするのですが、このスピンドルの穴の径で使える刃がきまります。
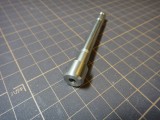
スピンドルに刃を差し込んで芋ねじで固定するのですが、スピンドルの径ちょうどの刃を使わないといけません。しかし、刃によってこの径が 6mm, 4mm, 3.175mm, 3mm と様々です。(iModela はハンドリューターサイズの2.35mm)
刃の軸径に合わせてスピンドルを用意しそれを差し替えるのが推奨されている使い方となります。
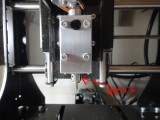
しかし、スピンドルはスピンドルホルダーに取り付けられフライスに固定されているため、交換するにはZ軸をほとんどばらしてまた組み立てるという作業が必要になってしまいます。
そこで私は径変換のスリーブコレットを利用しています。
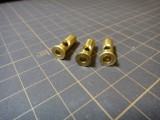
コレットを使うと偏心する可能性があるため推奨ではないのですが手軽に径の違った刃を交換できるようになります。
私はキデッジショップさんで購入したのですが、現在は在庫なしになっているようですね。探してみると同様のコレット(もしくはスリーブという名称)で扱っているところがいくつか見つかりますのでそういったところで在庫があるところから買い求めるとよいのではないかと思います。
今使っている刃だと、ドリルと美濃昌典が 3mm 軸、エンドミルが 4mm 軸なのでこの二種類があれば事足りている次第。
オリジナルマインドさんは、この軸の違いを考慮してできるだけ1本の刃で交換なしに仕上げるようにという方針の様子。「土佐昌典」シリーズはそういうコンセプトの刃。これだとスピンドル径が一つで済むからね。
他の刃を使いたい、特にエンドミルを使うところをどうにかすれば 3mm 軸一本で済ますことができるかもしれません。
posted by
rerofumi
2012/4/14 土曜日 23:20:13
■ プリント基板CAD
回路図が書けて何を作るかが決まったところで、今度はその回路をプリント基板に起こします。
プリント基板のパターンを設計するためには専用のプリント基板CADがあるのでそれを利用します。CNCでプリント基板を作成する際はガーバーデータを介して出力しますので、ガーバーデータを作成できるCADであることが必須の条件になると思います。
プリント基板設計CADにも色々種類があり特徴もそれぞれですので、手になじんだ物を使うと良いでしょう。
私はちょくちょく出てきているように K2CAD を使用しています。あまりメジャーではないと思います。
K2CAD を選んだ理由は、
- サイズ制限が無い
- レイヤー数が127まである
- 商用利用に制限が無い
- ラッツネットを備えている
- 「P板.com」さんでの出力実績がある
- シェアウェアとして安価である(3150円ほど)
といったところが良かったからで、悪いところは
- マニュアルの整備が不十分で使い方がわかりにくい
- 不安定でクラッシュすることが多い
- ライブラリが無く自作する必要がある
とまあ割と致命的な感じもします。それでも使うのは玄人肌というか、苦労を楽しむというかそんな方向かもしれません。
しかし、基板を製作して MTM とかで販売しようと考えたときにそれは商用利用かどうかというのは割と悩むところです。特に EAGLE LIGHT はサイズ制限だけでなく商用不可というライセンスなのがどうにもひっかかり鞍替えすることにしました。
昔色々なCADを一通り試したところ個人的な要望は「オートルーターは使わない(使えない)けれどもラッツネットは欲しい」というあたりに落ち着きました。しかし、アマチュア向けでラッツネット対応のCADはあまりなくてその頃唯一使えた K2CAD にたどり着いたといった流れでした。
ここでは私の実作業例として K2CAD を使った手順を記載します。
Read the rest of this entry »
posted by
rerofumi
2012/3/31 土曜日 16:47:06
第三回『回路図の作成とネットリスト』
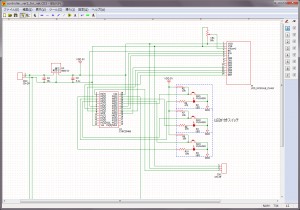
■ 回路図を書きましょう
ユニバーサル基板での工作に慣れてくると「取りあえず作りながら回路を考える」ということをやりがちになってしまいます。
それはそれで完成するため問題は無いのですが、完成した物が本当に一点物になってしまい現物以外シェアするものがなくなってしまいます。
電子工作において成果の共有を考えたときに最も基本になるのが回路図だと思います。これを発表し、共有すれば他者が同じ物を作成したり、参考にしてさらに発展させたものを作ったりできるようになるのです。
なので回路図が無い工作は世界に対して広がりを持ちません。できるだけ回路図を書きましょう。
また、CADやCNCを使ったプリント基板製作は、デジタルで設計した物がそのまま実態として製造できるといったメリットと楽しさがあります。その代わり「設計してから製造」といった作業フローに対して厳格です。
いきなり作り始めたいところをぐっとおさえて、最初に設計を行うという手順に慣れてください。
デジタルで設計さえしておけば、いろんな方法で具現化ができるという時代になってきています。電子工作、マイコン工作で最初に設計するものは何かと言ったら回路図なのではないでしょうか。
■ 回路図の作成
私は回路図の作成にはフリーウェアである BSch3V を使わせて貰っています。
Read the rest of this entry »
posted by
rerofumi
2012/3/19 月曜日 2:19:07
第二回『データの種類とアプリケーション』
■ 沢山の過程と中間ファイル
CNCフライスでのプリント基板作成をするためには、プリント基板の設計データが必要になります。
そのプリント基板設計データはデジタルデータですのでPC上のアプリで作成するのですが、実際に工作機械で製作をするためにいくつものアプリケーションと中間のデータが必要となってきます。
途中途中のデータの形式とそれが必要な理由を理解することで、作業フローを把握しましょう。
■ 製作フロー
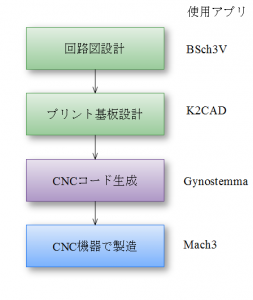
上のフロー図は私がプリント基板作成のために行う作業とそこで使うアプリケーション名です。
直接プリント基板設計から入り回路図を作成しないということも可能なのですが、より正確な設計を行うため、またドキュメントを残すためできるだけ回路図設計から入るのが良いと思います。
おおざっぱではありますが、この手順で作業をしていることを理解してください。
■ アプリケーションとデータフロー
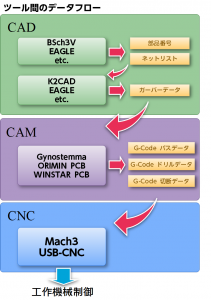
作業ではなく、アプリケーションと中間生成データを軸とした図に書き直したものがこちらです。
使用するアプリケーションは大きく分けて3種類で、CAD/CAM/CNC と呼ばれています。
CAD は設計部分です。回路図の設計とプリント基板のパターン設計を行います。最近は回路図設計とパターン設計がセットになって一つの CAD アプリとなっているのが主流となってきています。
BSch3V や K2CAD/D2CAD はその二つが分かれている形ですね。
CADによって最終的に生成するのはプリント基板のパターン形状を表したガーバーデータと呼ばれる形式です。それとドリル穴を開ける位置を示したドリルコードも含まれますが、纏めてガーバーと呼ぶことがあります。
プリント基板の製作会社に製造を依頼する場合は、このガーバーデータを納品して作って貰います。プリント基板の設計書といったところですね。
私は K2CAD で設計する際に、BSch3V で設計したネットリストを利用します。これはパターン設計の時にまた説明します。
ガーバーデータがパターンの設計書になるわけですが、どのように機械を動かせばその設計書通りの物が製造できるかを計算するのが CAM アプリになります。拙作の Gynostemma がこれにあたります。
プリント基板製造では、CNCフライスでどのように刃を動かせばパターンが掘れるかといった切削パスを計算する作業を行います。
プリント基板の設計書であるガーバーデータを読み込んで、機械の動きを指示する G-Code を生成するといった作業を行います。立体加工とかでは、立体モデルデータを読み込んで掘り出すための切削パスを生成するといった働きをします。
個人やフリーで利用できる CAM アプリがあまりなく、プリント基板製作用には cam.py がありましたが入力データ形式に制限があったりと色々問題がありました。
最近は Gynostemma だけでなく、有償の OriminPCB や WINSTAR PCB など個人でも購入できるプリント基板製作 CAM が出てきたため幾分やりやすくなっているのではないかと思います。
切削パターンの G-Code が作成できたら CNC アプリで工作機械を制御して実際にプリント基板の作成を行います。CNC アプリに G-Code を読み込ませることで加工をしますので、G-Code次第でいろんなものが作れるというのが一般的な様です。
なお、WINSTAR PCB は CAM+CNC という位置づけのようです。
最終的に必要なのが G-Code や CNC 駆動ですので、CADでの設計から直接それが生成できるのであればそれで十分ですしそういったツールもあるようです。
posted by
rerofumi
2012/3/8 木曜日 0:41:42
第一回 『プリント基板をつくるには』
前知識。
最近の電子工作は半田付けの要らないブレッドボードのおかげでずいぶんとお手軽になりました。そのおかげでマイコンを中心に電子工作人口も広がったように感じます。
ですが、ハンダごてを握ってプリント基板に部品を半田付けしていく形式の電子工作も捨てがたいものがありますよね。プリント基板を使うと製作物が固定されたものになりますので、ケースに組み込む等作品として完成させる楽しみに繋がっていきます。
個人製作の一点ものである場合はユニバーサル基板を使うのが手軽で一般的ですが、配線が面倒という問題があります。
そこで自作のプリント基板が次のステップとして現れてきます。
プリント基板を自作することにより
- 配線の手間を省略することができる
- 適当なサイズに纏めることができる
- 面実装部品を使う事ができる
といったメリットを享受することができます。
特に面実装部品は重要です。最近のマイコンやデジタル部品はフラットパッケージのものが多くなってきました。ちょっと気の利いた工作をしようとしたら面実装部品を避けて通ることができません。
そういった特殊な部品を使いこなして工作の幅を広げるためにも自作プリント基板にチャレンジしてみませんか。
Read the rest of this entry »